Our Process
Understanding your processes and equipment is foundational to our approach. We listen differently. We want to understand your situation, challenges, and objectives.
We begin with a performance assessment, root cause analysis, or compliance review to understand what problems or opportunities for improvement exist, as well as your compliance, reliability, and production goals. Our propriety software is used to model situations, process improvements, and performance improvements. Our objective is to provide you with the most cost-effective improvement strategies that meet your needs, whether they are performance, economic, or production driven.
Neundorfer is not a typical consulting firm. We provide you with comprehensive, quantitative, and actionable information that is created from the powerful combination of experiential knowledge, broad technical knowledge, and a strong analytical process. We deliver the tools you need to make informed decisions about capital, maintenance, operations, and fuel or process changes so you can stay focused on your objectives.
Whether you are looking to reduce costs, reduce energy consumption, optimize performance, reduce emissions, or improve safety, reliability or efficiency, our process will support your analysis and decisions.
Applications
We excel at finding the low-hanging fruit that yields the greatest benefits. Through our thorough technical analysis, we know what results to expect from any individual tactic or combination of tactics. We can apply this process across your plant while employing our comprehensive KnowledgeBase, modeling, and analytical capabilities.
We consistently meet or exceed our customers performance expectations. Give us a call. We are happy to share the results of this process with you.
Changing the Future
Modeling potential scenarios allows you to see into the future so that decisions you make are based on the anticipated results of process changes, equipment improvements, and operational improvements. This identifies paths forward, builds confidence in decisions, and allows for impactful actions to be taken. These tools support asset management decisions, compliance projections, and provides insights into complex engineering and operating options.
All of our predictive modeling expertise resides in house and includes emissions equipment performance modeling, computational fluid dynamics (CFD) modeling, and scale physical modeling of equipment. We integrate proprietary software, consulting and engineering expertise, and field experiences into the modeling process to help customers analyze the right data to solve problems faster and more effectively. By integrating our implementation experiences, we can help you make decisions that take into account time, budget, and performance.
What We Do
We can use performance modeling to help you:
- Make asset-related decisions based on scenario planning
- Create real-time and historical particulate emissions equipment performance modeling
- Model air quality control system performance to predict future scenarios, to make improvement decisions, and to create operational strategies
- Measure and optimize fabric filter bag life
- Make decisions about fuel switching or identify impacts to air pollution control equipment and the associated changes that should coincide with a fuel switch
- Make decisions around additives or sorbent injection systems including the type of sorbent used, injection placement and rates, and identify impacts on air pollution control equipment
- Reduce energy consumption
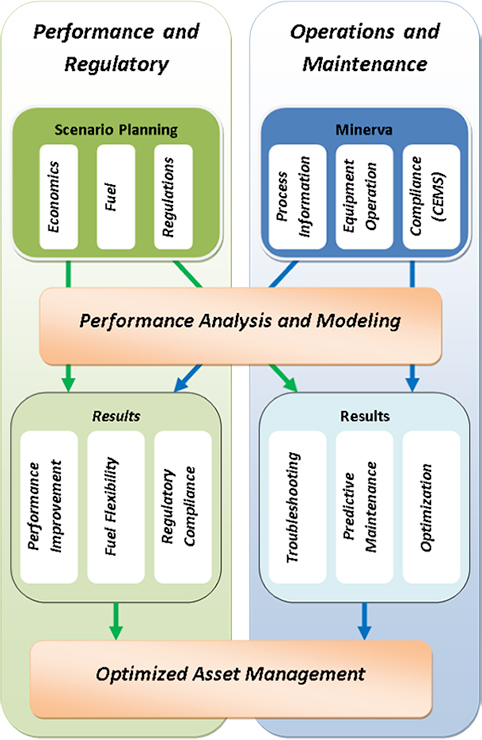
Files & Resources
- Page
- Paper Mill Gains Operational Flexibility While Reducing Emissions
- View Page
- Page
- Results-Driven Decisions, Remarkable Results
- View Page
- application/pdf
- FuturePowerTechnology_Dec2016
- View File
- application/pdf
- ProcessOptimizationBrochure_09252017
- View File
- Troubleshooting Plant Systems
- View Document
- Process Optimization
- View Document
- Steel Reheat Furnace Optimization
- View Document